現行品と同じく架橋発泡体のフォームを用いた仕様でもご提案。左のグレーの素材「サンペルカ」も、圧縮強度や耐油性・耐水性に優れた素材ですが、今回は、より薄くて強度があり、狭い支持面積で製品を固定できる図Aの仕様に決まりました。
アルミダイカスト部品通い箱内装
自動車を構成する部品は無数に存在し、その一つひとつが、製造工場から組み立て(アッセンブリ)工場へと輸送されます。それらのうち、エンジンや給排気系統に用いられる金属部品の多くは、その複雑な形状や要求される強度のシビアさなどから、アルミダイカストという鋳造製法と、その後の切削加工で仕上げられます。こうした金属部品の多くは、入り組んだ立体形状と、鋭い切削面を持つことから、高度な輸送上の配慮が必要とされます。
現行品の梱包形態と問題点
固定材(発泡体)とダイカストの切削面が接触し出し入れ時や輸送中の摩擦で磨耗してしまう
まずは現行品の画像から。写真の中央に白く柱状に見えるのが、製品を支持する固定用の内装材(架橋発泡体)です。お客様からご相談を受けたのは、オレンジの点線枠内の部位。固定材の柱に、ダイカスト部品の切削面がじかに触れてしまうため、製品を出し入れする際や輸送中に、発泡体が損傷・磨耗してしまうというものです。
生出からの改善提案
詳しくお伺いしてみると…
実はこんなにありました「触れてほしくない部位」
今回の輸送資材の見直しを機に、気になる部位や課題を色々とお伺いした所、上記の切削面の他にも、固定材に触れることを避けた方が望ましいという部位が、下図Aのように浮かび上がりました。また、現行の通い箱は製品6個収納する仕様でしたが、輸送上のコストパフォーマンス向上のため、外装箱は同サイズのまま、入り数を増やせれば尚望ましい、とのご要望も頂きました。現行品に似たグレーの発泡体を用いた仕様(下図B)でも設計させて頂きましたが、より磨耗に対する耐久性が高く、コストパフォーマンス的にも優れることなどから、最終的には低発泡シート(→「低発泡シート」のページへ)を用いた下図Aの仕様に落ち着きました。
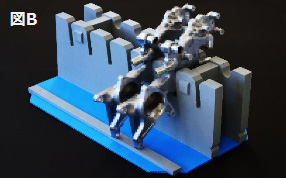
効果測定
改善効果 | |
---|---|
物流効率 | 16.7%向上 (入り数6→7) |
資材耐久性 | 製品支持部位の磨耗・損傷を解消 |
設計技術担当者からのコメント
今回は、従来の業者ではヒアリングしきれていなかった困りごとを色々とお伺いでき、お客様の課題により密着したご提案ができました。図Aにあるようなご要望や入り数の向上、コストパフォーマンス改善など、品質とコストの両面から、お客様の課題解決に向けたご相談に乗らせて頂きます。現行の梱包業者で対応が難しい問題などがありましたら、ぜひ生出にご相談下さい。